Hi ha molts tipus de làmines de plàstic amb una àmplia gamma d'usos. Actualment, els principals tipus són el clorur de polivinil, el poliestirè i el polièster (PET). La làmina de PET té un bon rendiment i compleix els requisits d'índex d'higiene nacional per als productes modelats i els requisits internacionals de protecció del medi ambient. Pertanyen a la taula de protecció del medi ambient. Actualment, els envasos han de complir els requisits de protecció del medi ambient i reciclatge, de manera que la demanda de làmines de PET és cada vegada més gran. Aquest article tracta principalment el procés de producció i els problemes comuns de les làmines de PET.
Tecnologia de producció de làmines de PET:
(1) Full de PET
Com altres plàstics, les propietats de la làmina de PET estan estretament relacionades amb el pes molecular. El pes molecular està determinat per la viscositat intrínseca. Com més gran sigui la viscositat intrínseca, millors són les propietats físiques i químiques, però poca fluïdesa i dificultat de formació. Com menor sigui la viscositat intrínseca, pitjors són les propietats físiques i químiques i la resistència a l'impacte. Per tant, la viscositat intrínseca de la làmina de PET hauria de ser de 0,8dl/g-0,9dl/g.
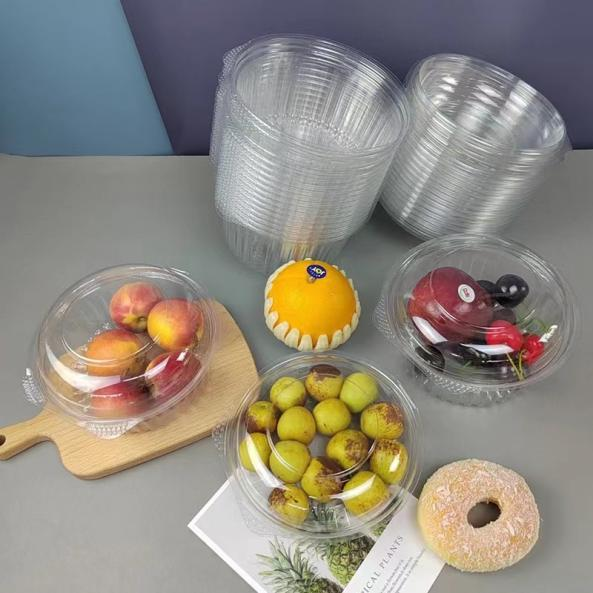
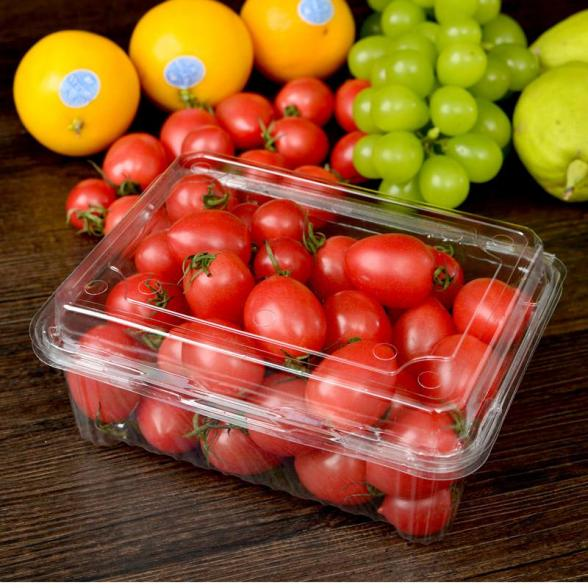
(2) Flux del procés de producció
El principalequips de producció de làmines de PETinclou torres de cristal·lització, torres d'assecat, extrusores, capçals de matriu, calandres de tres rodets i bobines. El procés de producció és: matèries primeres cristal·lització-assecat-extrusió plastificació-extrusió modelat-calandrat i modelat-bobinat.
1. Cristal·lització. Les rodanxes de PET s'escalfen i cristal·litzen a la torre de cristal·lització per alinear les molècules i, a continuació, augmenten la temperatura de transició vítrea de les rodanxes per evitar l'adhesió i l'obstrucció de la tremuja durant el procés d'assecat. La cristal·lització és sovint un pas essencial. La cristal·lització triga 30-90 minuts i la temperatura és inferior a 149 °C.
2.Seca. A altes temperatures, l'aigua s'hidrolitzarà i degradarà el PET, donant lloc a una reducció de la seva característica adherència, i les seves propietats físiques, especialment la resistència a l'impacte, disminuiran a mesura que disminueix el pes molecular. Per tant, abans de fondre's i extruir, el PET s'ha d'assecar per reduir el contingut d'humitat, que hauria de ser inferior al 0,005%. L'assecador de deshumidificació s'utilitza per assecar. A causa de la higroscopicitat del material PET, quan l'aigua penetra profundament a la superfície de la llesca, es formaran enllaços moleculars i una altra part de l'aigua penetrarà profundament a la llesca, dificultant l'assecat. Per tant, no es pot utilitzar l'aire calent normal. El punt de rosada de l'aire calent ha de ser inferior a -40ºC i l'aire calent entra a la tremuja d'assecat a través d'un circuit tancat per a l'assecat continu.
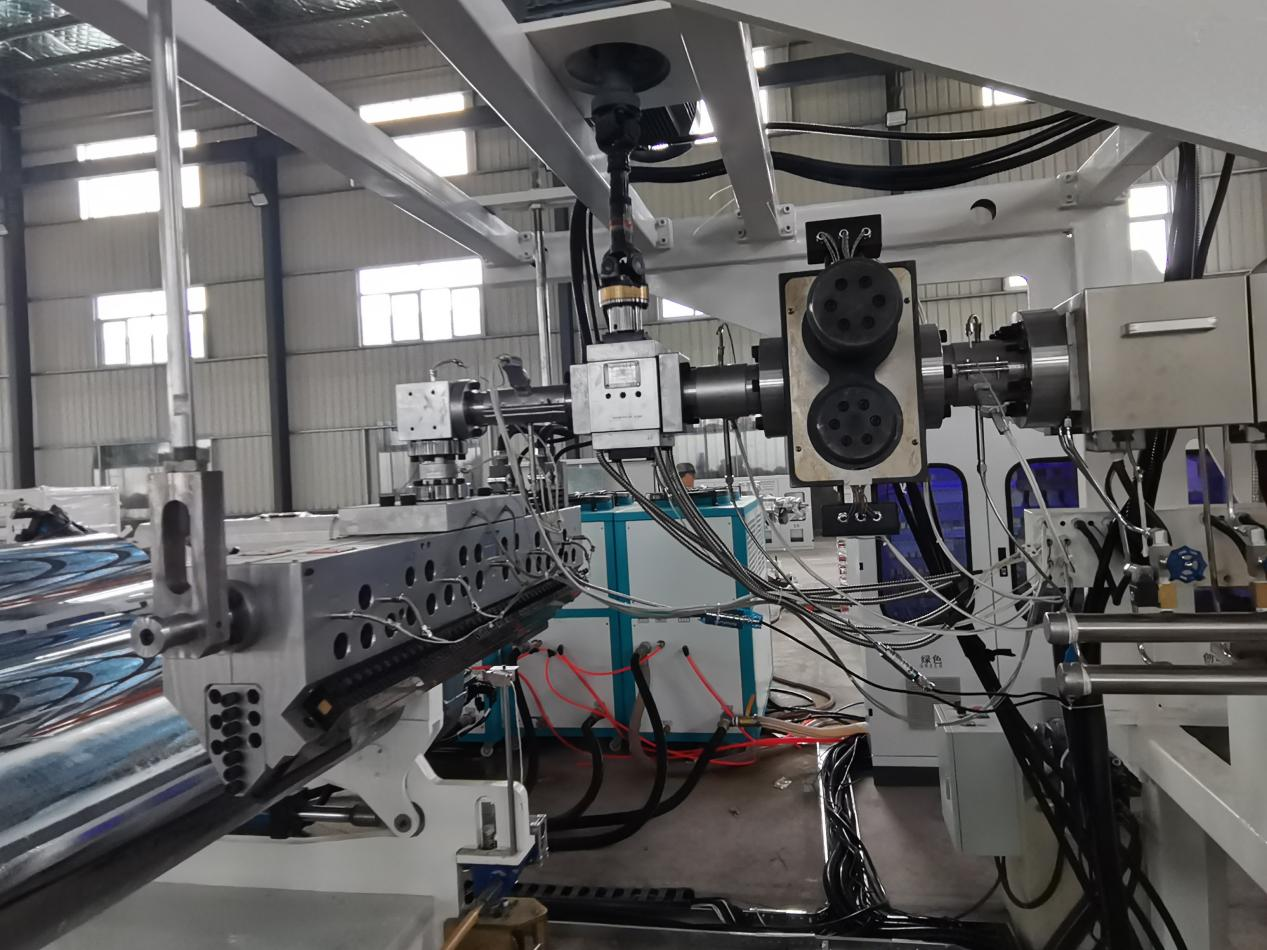
3. Premeu. Després de la cristal·lització i l'assecat, el PET es transforma en un polímer amb un punt de fusió evident. La temperatura de modelat del polímer és alta i el rang de control de temperatura és estret. S'utilitza un cargol de barrera específic de polièster per separar les partícules no foses de la fosa, cosa que ajuda a mantenir un procés de cisalla més llarg i augmenta la producció de l'extrusora. Adopta una matriu de llavi flexible amb vareta d'acceleració aerodinàmica. El cap del motlle és cònic. Els corredors aerodinàmics i els llavis de matriu sense rascades indiquen que l'acabat ha de ser bo. L'escalfador de motlles té funcions de drenatge i neteja.
4.Refrigeració i conformació. Després que la massa fosa surt del cap, entra directament a la calandra de tres rotlles per calandrar i refredar. La distància entre la calandra de tres rodets i el capçal de la màquina generalment es manté en uns 8 cm, ja que si la distància és massa gran, el tauler s'arrugarà i s'arrugarà fàcilment, donant lloc a un acabat deficient. A més, a causa de la llarga distància, la dissipació de calor i el refredament són lents i el cristall es torna blanc, cosa que no és propici per a rodar. La unitat de calandrat de tres rodets consta de rodets superior, mitjà i inferior. L'eix del corró mitjà és fix. Durant el procés de refrigeració i calandrat, la temperatura de la superfície del rodet és de 40 °C-50 °C. L'eix dels corrons superior i inferior es pot moure cap amunt i cap avall.
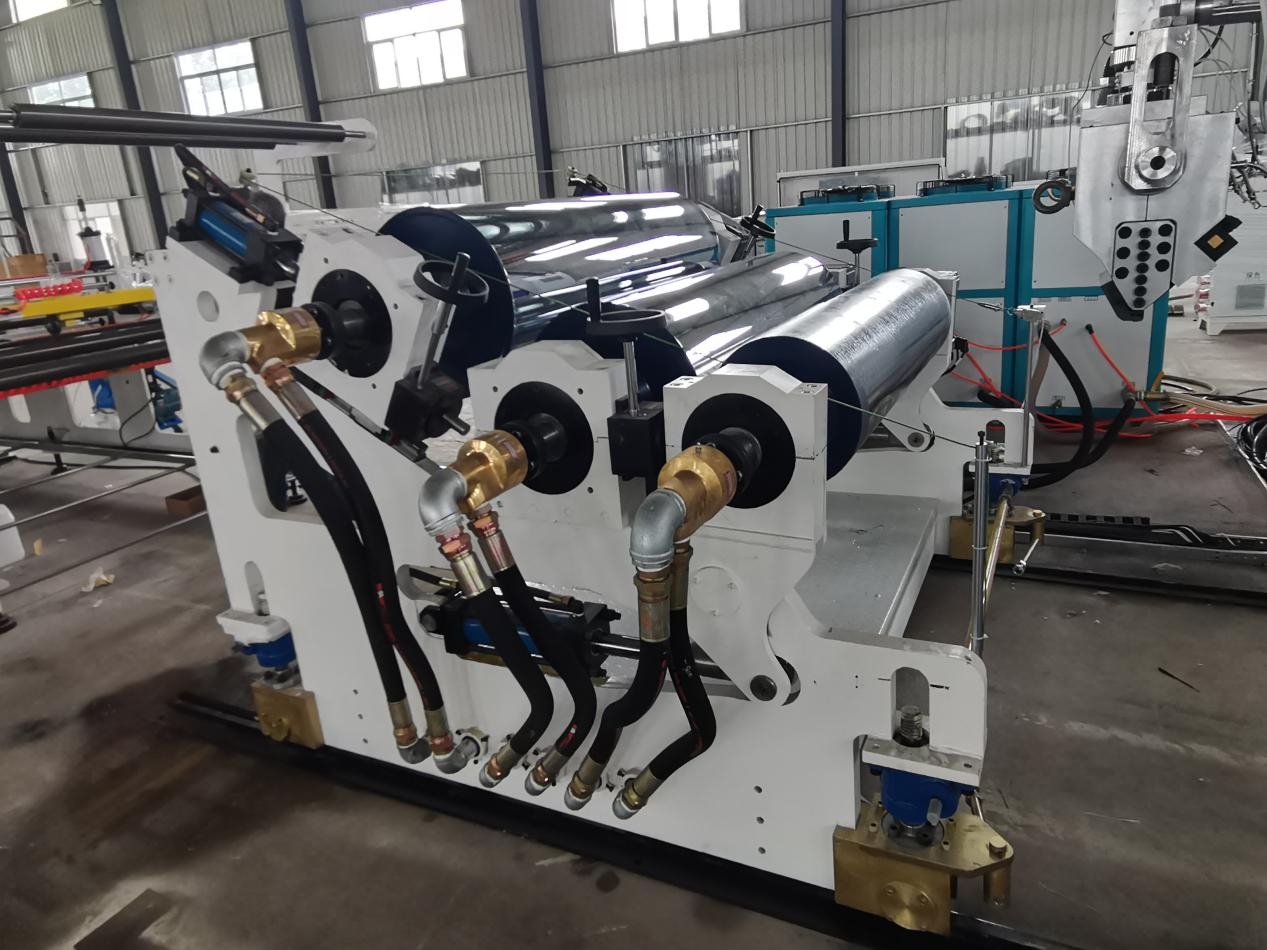
Hora de publicació: 28-set-2023